Turbine trip interlock
The turbine is monitored throughout the process to safeguard it in case of emergency. As high-pressure steam is used to run the turbine the shaft rotates above 3000 rpm as per its design. Hence rotating at that speed there is a possibility of hazard to happen to eliminate that the Turbine Supervisory system keeps on monitoring important parameter related to the turbine and implement turbine trip command in case of an emergency.
You may aware of the trip condition of the turbine, in case any trip condition reached. We will get an alarm before the trip and even after that setpoint the parameter is not under control reaches the High High level then the trip circuit will shut down the process. By this example let’s see how the signal travel from the field to the trip circuit.
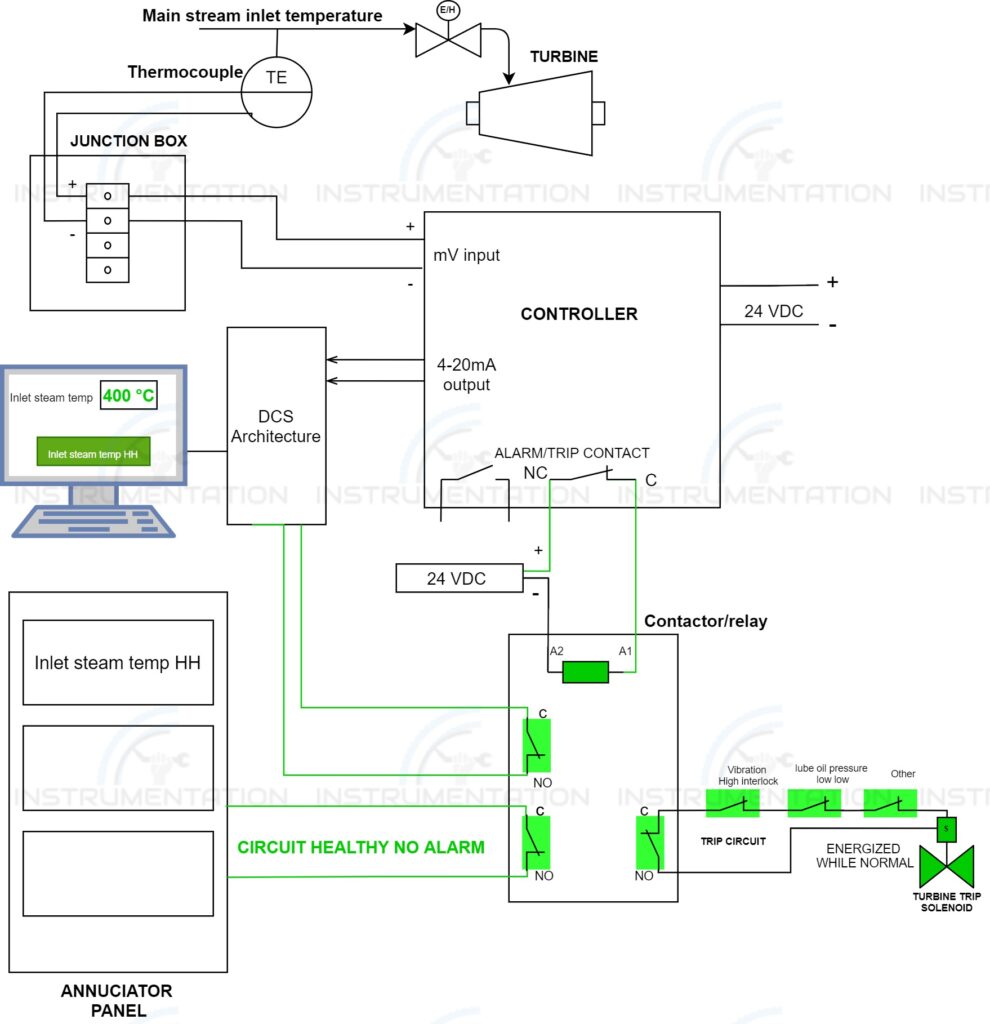
In the above diagram, you can see how the temperature element(Thermocouple) measures the temperature of the steam and transmit the MB to the controller. The controller senses the mV converted into 4-20 mA to transmit to DCS for real-time monitoring.
The controller has several contacts to use as per our requirement. The contact can be programmed as per our requirement to drive an annunciator, trip, alarm and interlock, etc.
The contacts in the controller will be Normally closed conditions below 500°C. And hence the contactor coil will be energized by the positive supply switched through the controller relay port. once the temperature reaches the setpoint the contact will change to Open condition breaking the supply flow to the contactor. As the contactor gets de-energized the alarm, trip, annunciator connected with the contactor port will get triggered.
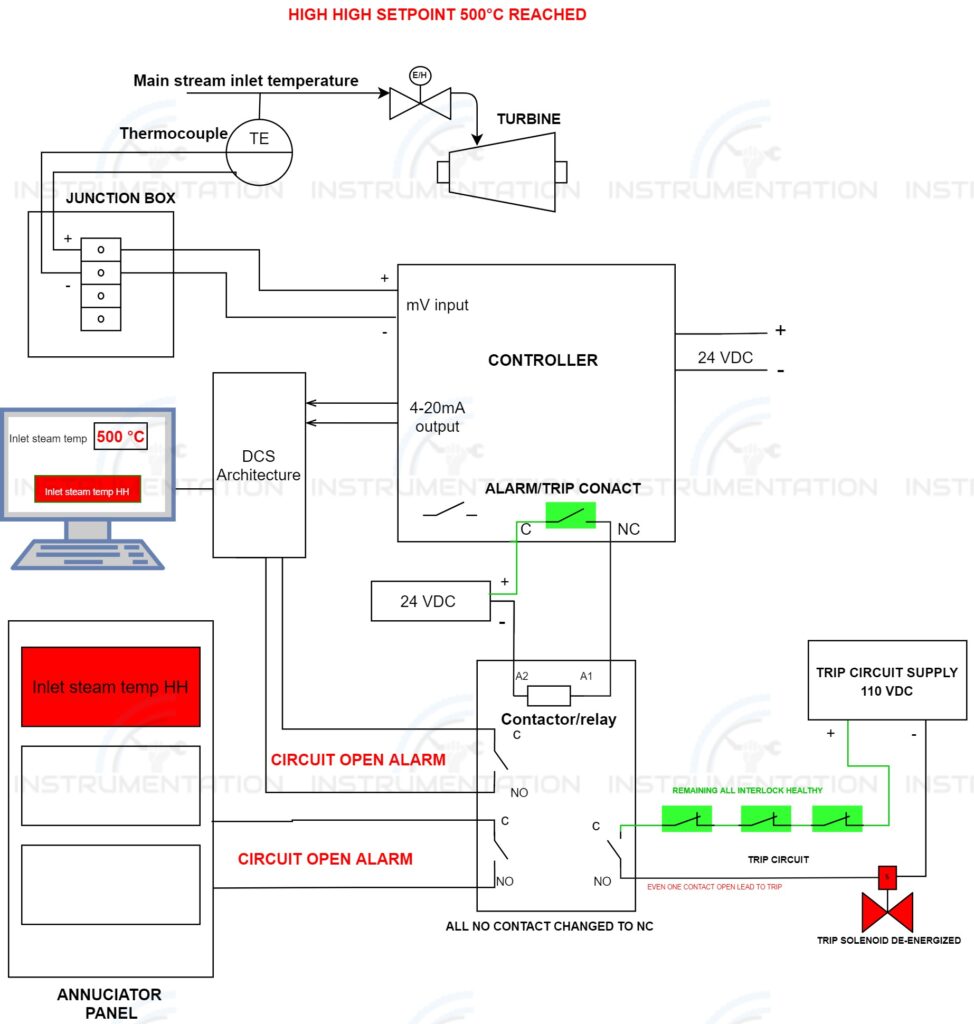